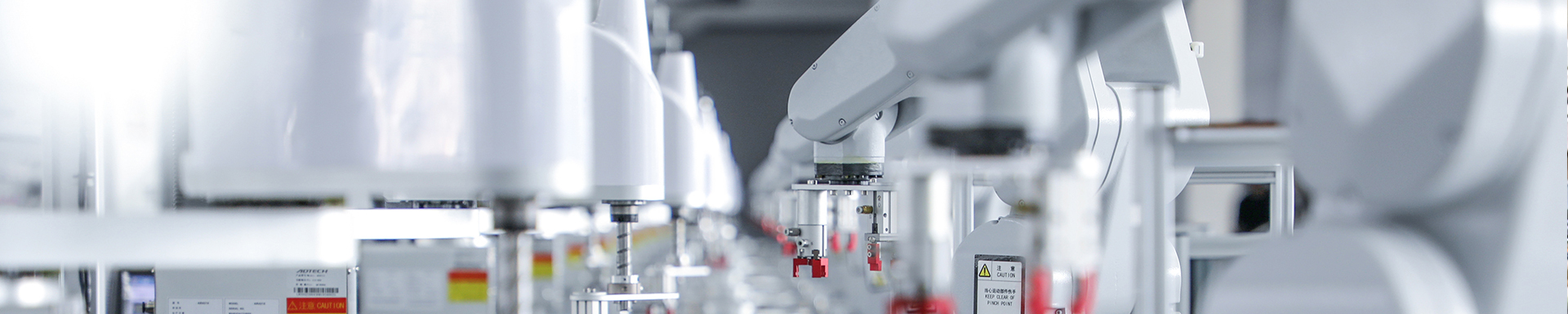
Flat Bottom Bag With Zipper
Use less film, but hold more: It's hard to find an advantage over packaging that uses less material while creating more space for the product. Because flat-bottom bags use 12% less film but have a larger capacity, they require less energy and weigh less. Both of these factors reduce costs and make it better for our environment.
No Outer Boxes: These bags are designed to eliminate the need for an outer box, reducing costs.
Replacing the inner layer: As part of the bag design, the lamination of different types of materials makes this possible.
They also have a resealable zipper that really works: this is obviously a more useful and fun way to handle pouches and many other product types.
Side inserts mean more print space: the extra space can be put to good use to help brand and sell products.
Flat bottom is safe and stable: easy to store and display on supermarket shelves.
- OEM & ODM
- China
- 5 DAYS
- 600000 PCS
- Information
Product Name | Flat Bottom Bag With Zipper |
MOQ | 2,000 pieces |
Material | PET12/VMPET/PE80 |
Total thickness | 140micron |
Size | 150mm width x 230mm height + (35x2)mm bottom gusset |
Features | 1). Made with superior quality 100% recyclable material. 2). Food grade laminate interior for barrier protection against oxygen, odors, and moisture. 3). Durable resealable zip lock closure. 4). Easy-to-open tear notches. 5). Heat sealable to create a tamper-evident, retail ready finish. |
Usage Field | Snack, milk powder, beverage power, nuts, dried food, dried fruit,Seeds, coffee, sugar, spice, bread, tea, herbal, wheat, washing powder, salt, pet food, candy, rice, clothes etc. |
Payment | TT, VISA,Paypal,Western Union,Trade Assurance |
Lead Time | 10-25 working days according to order quantity |
Common materials for flat bottom bags
1. Double-layer plastic-plastic composite film:
polyester/polyethylene PET/PE, nylon/polyethylene NY/PE
Applicable: General packaging, no need to cook at high temperature, and the contents can be displayed transparently.
2. Double-layer plastic-plastic high-temperature cooking film:
polyester/polypropylene PET/CPP, nylon/polypropylene NY/CPP
Application: high temperature cooking, resistant to high temperature above 110℃-120℃. Contents can be displayed transparently.
3. Three-layer aluminum-plastic composite film:
Polyester/Aluminum/Polyethylene PET/AL/PE Nylon/Aluminum/Polyethylene NY/AL/PE
Polyester/Aluminum/Polypropylene PET/AL/CPP Nylon/Aluminum/Polypropylene NY/AL/CPP
Applicable: High-grade packaging, protected from light, and does not display the contents.
Determine some basic information of the flat bottom bag, mainly including the material, thickness, bag type, size and other requirements of the eight-sided packaging bag. This is also what you need to know when customizing other types of packaging bags.
The design of the flat bottom bag is based on the needs of the customer, and the designer or the packaging bag manufacturer can design and produce it. When designing, it is necessary to provide required printing information, design themes and elements, etc. Novel and creative design can attract attention, help promote the brand and increase sales.
For the plate making of the flat bottom bag, the plate making is directly related to the color printing effect of the eight-side sealing bag. If you want to make a beautiful packaging bag, you must make a fine printed copper plate. The plate making is based on the design manuscript, and the quantity is also determined by the manuscript.
For color printing of flat bottom bags, after the plate is made, the copper plate is loaded on the printing machine. Color print the design of the eight-side seal bag onto the first layer of material. The requirement of color printing quality is that there should be no color difference.
The material of the flat bottom bag is compounded, and the material films of different functions such as printing materials, barrier materials, and heat sealing materials are compounded together.
For the curing and curing of the flat bottom bag, after the material is compounded, the composite strength is not stable, and it cannot be used immediately. It needs to be cured and cured. Generally, it is put into a constant temperature curing room for 24-48 hours, so that the moisture and solvent in the adhesive can be fully volatilized.
For the sub-roll bag making of the flat bottom bag, after curing, the customization of the eight-side sealing bag is basically completed.